In pharmaceutical manufacturing, viscous drug products pose unique challenges to filling efficiency and accuracy.
This article explores the operational mechanics and methods best suited to certain viscosity ranges, including considerations for pump and tubing selection, pressure settings, and how to address additional challenges or complexities, such as working with non-Newtonian fluids.
Peristaltic or piston pump?
The main challenge in manufacturing viscous solutions is efficiently moving the solution through the filling line. While traditional methods often use peristaltic pumps, which gently massage the tubing to push product through, their effectiveness decreases with higher viscosity solutions, akin to siphoning honey through a straw. For more viscous substances, piston pumps, suitable for solutions over 100 centipoises (cP), are preferred for their mechanical efficiency.
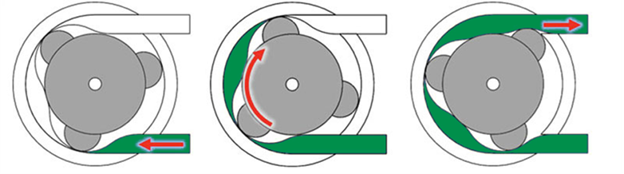
Piston pumps consist of a piston, a chamber, and two valves. The pump drives the piston up to create a strong vacuum to pull in solution through the inlet valve. Once the piston has reached its maximum height, it will shut the inlet valve and open the outlet valve that leads to the filling needle by turning the piston. Then the piston moves down to squeeze the solution out of the chamber and through the outlet valve. The outlet valve is then closed, and the inlet is opened, and the process repeats itself to deliver the next pump. The motion is simple, mechanical, and efficient at moving viscous solutions through tubing.

When to add pressure
In many cases, using a piston pump alone is not enough to efficiently fill viscous drug product. Once the viscosity exceeds 1,000 cP, it may be necessary to add pressure to help push the drug product through the inlet to the pump and fill the pump. If this is the case, the drug product will be sterile filtered into a pressure vessel. Then, during filling, a sterile gas will be pumped into the vessel to pressurize it and help push product through the fill line.
If the system is pressurized, it will be necessary to use pressure-rated tubing (either reinforced tubing that is threaded to prevent bulging or rigid tubing) to connect the pressure vessel to the piston pump. The tubing must be rated for the maximum pressure that the system may experience, otherwise an overstressed system can cause a leak or break in the line that can result in drug product loss, a sterility risk, or may endanger the operators.
Avoid bulging with reinforced tubing
Selecting pressure-rating tubing is not only important when the system is pressurized, but it also plays a role in filling accuracy and consistency. If the drug product is highly viscous, it can cause bulging in the tubing when the piston drives drug product out of the chamber. The bulging eventually relaxes back to its original size, causing variable fill volumes and potentially spilling on the outside of the containers if the fill needle continues to dribble as the new containers are repositioned under the fill needle. To prevent bulging, fortified tubing should be selected for the outlet of the fill line assembly (the tubing connects the pump to the fill needle).
The ideal fill setup based on viscosity
As a rule of thumb, if the drug product is <100 cP, then a fill will typically involve a bioprocess bag or glass vessel and a peristaltic pump connected by silicone tubing.
If the drug product is between 100 – 1,000 cP, then the fill will most likely involve a bioprocess bag or glass vessel and a piston pump connected by silicone tubing for the inlet and reinforced tubing for the outlet.
If the drug product exceeds 1,000 cP, then a pressure vessel may be used with pressure-rated tubing connecting it to a piston pump and reinforced tubing for the outlet.
Optimizing pump speed
To determine the necessity of a piston pump for a product, a simple fill study is conducted using a peristaltic pump. The process begins at a slow speed, filling a limited number of containers and subsequently performing weight checks on each filled unit. The pump speed is incrementally increased, with continuous monitoring and recording of weights, until it’s observed that the weight checks begin to fall. This occurs when the pump speed outpaces the viscous product’s ability to fill the pump. The average dispensed volumes (weight checks) at each set pump speed are then charted to determine the maximum speed at which the pump can run at before dispensed volumes decrease.
If this maximum speed is deemed too slow for practical application, then this suggests the peristaltic pump is ineffective for the product’s viscosity, and the CDMO will consider employing a piston pump. The piston pump, known for pulling a more effective vacuum, is then tested under similar conditions to ascertain if it can fill the product more efficiently on its own. If the optimal pump speed is still too slow, then the CDMO may look at adding a pressure vessel to help fill the chamber faster.
Reducing stress in your filling process
To efficiently move viscous solutions through the fill line, overcoming tubing drag is essential. Drag increases with longer tubing lengths or smaller diameters, leading to a pressure drop from the pressure vessel to the pump inlet, which reduces the effectiveness of the process. Reducing this pressure drop minimizes system stress and enhances safety and efficiency of the method. Adjusting tubing lengths and increasing inner diameters can significantly reduce drag. For instance, if efficient filling requires 10 psi at the pump and the initial pressure drop is 40 psi, setting the vessel to 50 psi is necessary. However, optimizing tubing can lower the pressure drop to 20 psi, allowing the vessel to be set at 30 psi while maintaining the same fill efficiency.
Outsmarting bubbles
Air inside fill lines pose a significant issue in viscous filling. If the air bubble starts in a pressurized vessel, it will remain small until it reaches the piston pump where the pressure on the bubble drops significantly. Once the force is gone, the bubble will expand. This can cause dribble because the bubble will take time to completely expand in a viscous solution, and as it is expanding, it is pressing solution out of the fill needle. The bubble will also cause variable fill volumes once it travels to the fill needle.
Getting bubbles out of a viscous solution is challenging, which is why it is best to take preventative measures. Mixing should be done carefully to ensure bubbles are not formed in the solution. If bubbles do appear, and the product is slightly viscous, then we may be able to wait and allow the bubbles to reach the surface of the solution. If the product is highly viscous, then it may be necessary to apply a vacuum on the product to help pull the bubbles out of solution.
Adapting to non-Newtonian fluids
Non-Newtonian fluids, a fluid whose viscosity changes depending on the force it experiences, adds additional complexity to a project.
Shear thickening fluids become more viscous as the force applied to it increases (think cornstarch dissolved in water). Drug products that are shear thickening will require slower mixing during formulation and slower filling to effectively move it through the fill setup.
Conversely, shear thinning fluids become less viscous as the force applied to it increases. This is commonly observed in drug products with a high hyaluronic acid (HA) content. Drug products with this property are generally easier to manufacture compared to other viscous drug products, because once they begin to move, they require less force to keep them moving. Mixing is easier, and there is less stress placed on the system during filling. They also have a smaller pressure drop from the pressure vessel to the piston pump which means they will require less force from a pressure vessel to move the solution to fill the pump.
Conclusion
Sometimes, filling viscous drug products can be tricky. The choice between peristaltic and piston pumps, along with the considerations for managing pressure, tubing specifications, and the challenges posed by air bubbles and the unique properties of non-Newtonian fluids, are only a piece of the puzzle that these products create in pharmaceutical manufacturing. Understanding the nuances of each pump type and the intricacies of fluid dynamics is critical for optimizing production efficiency, ensuring product quality, and maintaining system integrity. By carefully selecting the appropriate equipment and techniques, manufacturers can navigate these challenges effectively, ensuring that even the most viscous or delicate of drug products are filled accurately and safely.
About Sharp’s services
Sharp is a leader in pharmaceutical packaging, clinical trial supply services and small-scale sterile manufacturing. For 70-plus years, we’ve provided solutions to pharma and biotech clients from Phase I trials through to commercial launch and lifecycle management. With facilities in the United States, United Kingdom, Belgium & the Netherlands and more than 30 clinical depots globally, covering every region of the world, our experience is your strength.