Many small changes can deliver a big impact.
Progress through collaboration
Sharp is one of eight co-founders of the Alliance to Zero, a supply chain collaboration, founded in June 2021, that represents the value chain for injectable pharmaceutical devices, including producers of glass, injectable moldings, labels, packaging equipment designers, packaging & assembly and end-of-life services.
Together with these partners we are working towards significantly reducing GHG emissions along this supply chain for injectable devices.
The first undertaking of the Alliance was a detailed product carbon footprint mapping exercise. The alliance engaged an independent sustainability consultancy to oversee the mapping of the injectable value chain, working with each company member on their contribution to GHG for the autoinjector. That work is complete, and the Alliance has developed a detailed Product Carbon Footprint (PCF) for the autoinjector, with the support of a sustainability consultancy.
Having completed the independently verified PCF calculation, we now know the total carbon footprint of the autoinjector is 774g CO2e. The next step was to break that footprint down by company, so each individual company knew what portion of carbon they contributed and where the hotspots were within their processes and materials.
Identifying our carbon hotspots
Sharp carries out the assembly, labelling and secondary packaging of the injectable device and now, through this PCF work we have established how much Sharp is contributing to the overall injectable footprint. We have the data granularity to identify where those carbon hotspots exist in our production processes. We were surprised to learn – given that we don’t contribute any physical materials or components to the injectable device – that Sharp is responsible for 112 gCO2e, or 19% of the total carbon footprint of the autoinjector.
The PCF analysis allowed us to target the priority areas for the most impactful reduction interventions. One such area was the plastic intermediary tray that is used to store the autoinjector device after it has been assembled, while it is held in cold storage before being transferred to production for labeling and packaging. This tray is not part of the final injectable product packaging and so – unlike the injectable device packaging itself – the functional and technical specifications for the intermediary tray are directed by Sharp.
Reducing plastics in our injectables packaging process
Sharp’s Hamont-Achel packaging facility specializes in the secondary packaging of injectable devices, specifically pens, autoinjectors and pre-filled syringes. Under the direction of site manager Guido Martens, the engineering team approached Bachmann, who supplies Sharp with APET trays, to begin a collaboration to investigate possible amendments to the tray composition to reduce its carbon footprint.
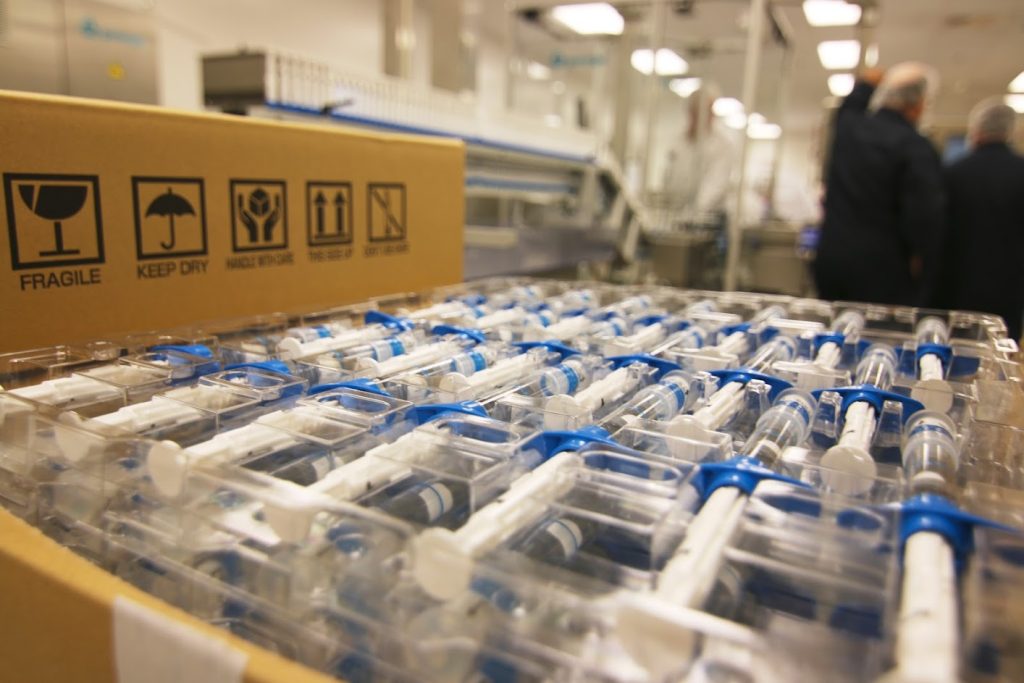
After some investigation, the team agreed to the following specification improvements for the new intermediary tray composition:
Reduced thickness
The overall thickness of the plastic tray was reduced by 10%. Initially, a 20% reduction was tested but ultimately not sufficiently strong enough for the purpose and a 10% reduction was agreed.
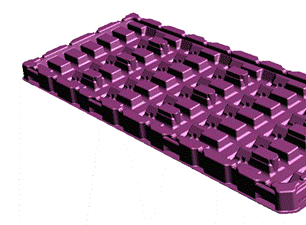
Introducing some rPET
The composition of the tray itself was modified to include a middle layer of rPET, with virgin PET on the outer and inner layers, in 10:80:10 proportion.
Extending reuse
The tray will also be used a minimum of five times before being sent for recycling. This reuse will be reviewed regularly with the intention of extending the trays reuse beyond five times, subject to them being regularly monitored and free of any contamination, cracks, etc.
Taken together, these changes meant a reduction of 38% in Sharp’s overall carbon footprint contribution to the autoinjectors PCF.
Sharp is committed to identifying & implementing innovative and pragmatic improvements to packaging materials, composition, and processes to reduce our GHG emissions and that of our clients, without compromising on quality.
We take great pride in being a leading partner to our biopharma clients with innovation, sustainability, and quality at the heart of our solutions. Connect with Hywel Woolf today, to discuss how we can collaborate on our sustainability journey.