Rob Feltz, Director, Analytical and Formulation Services, talks about techniques that reduce particle size.
A few weeks ago, I wrote about several formulation techniques that increase particle size, including roller compaction, high-shear granulation, and fluid-bed granulation.
Today, let’s talk about techniques that reduce particle size. But first, let’s refresh our knowledge of particle size and why it’s important.
Why Particle Size Matters in Drug Formulation
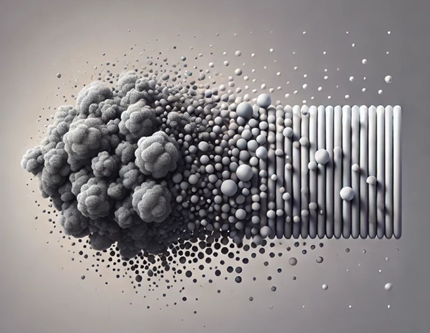
As particle size decreases, the surface area to volume ratio increases. This larger relative surface area enhances the dissolution rate and solubility of the particles, which can lead to improved bioavailability, especially for poorly soluble drugs.
Smaller particles are generally more easily absorbed through biological membranes in the GI tract. They can also penetrate tissues more effectively, potentially improving distribution throughout the body.
Particle size can also affect the stability of the drug. ๐ฆ๐บ๐ฎ๐น๐น๐ฒ๐ฟ ๐ฝ๐ฎ๐ฟ๐๐ถ๐ฐ๐น๐ฒ ๐๐ถ๐๐ฒ ๐น๐ฒ๐ฎ๐ฑ๐ ๐๐ผ ๐น๐ฎ๐ฟ๐ด๐ฒ๐ฟ ๐๐๐ฟ๐ณ๐ฎ๐ฐ๐ฒ ๐ฎ๐ฟ๐ฒ๐ฎ, ๐๐ต๐ถ๐ฐ๐ต ๐บ๐ฒ๐ฎ๐ป๐ ๐ถ๐ป๐ฐ๐ฟ๐ฒ๐ฎ๐๐ฒ๐ฑ ๐ฝ๐ผ๐๐ฒ๐ป๐๐ถ๐ฎ๐น ๐ณ๐ผ๐ฟ ๐ฟ๐ฒ๐ฎ๐ฐ๐๐ถ๐๐ถ๐๐ ๐๐ถ๐๐ต ๐ฑ๐ผ๐๐ป๐๐๐ฟ๐ฒ๐ฎ๐บ ๐ถ๐บ๐ฝ๐น๐ถ๐ฐ๐ฎ๐๐ถ๐ผ๐ป๐ ๐ผ๐ป ๐ฐ๐ต๐ฒ๐บ๐ถ๐ฐ๐ฎ๐น (๐ถ๐ป)๐๐๐ฎ๐ฏ๐ถ๐น๐ถ๐๐.
Techniques for Reducing Particle Size
During particle size-reduction, mechanical energy is imparted from the mill to the material in order to break it into smaller particles. The four most commonly used size reduction mechanisms are:
- Compression
- Cutting
- Impact
- Attrition
๐๐ผ๐บ๐ฝ๐ฟ๐ฒ๐๐๐ถ๐ผ๐ป is used for coarse reduction of large particles but is less effective for soft, elastic materials. It can also be difficult to achieve very fine particles sizes with this technique. Examples are roller mills and some conical mills.
๐๐๐๐๐ถ๐ป๐ด the particle size involves using sharp edges to shear the material as opposed to crushing or grinding. This method is good for elastic materials but poor for hard or brittle materials. May also be difficult to be achieve fine particle sizes. Examples: knife mills and some granulators.
๐๐บ๐ฝ๐ฎ๐ฐ๐ ๐บ๐ถ๐น๐น๐ถ๐ป๐ด reduces particle size by subjecting the material to high-speed hammers or similar tools. These mills are highly efficient but produce a wide distribution of particle sizes, so they may not be appropriate for some applications. Examples: hammer mills, jet mills.
๐๐๐๐ฟ๐ถ๐๐ถ๐ผ๐ป is a method that involves grinding and shearing particles against each other or a solid surface. It is suitable for creating fine and uniform particles but not for coarse size reduction. Examples are granulators and planetary mills.
Impact of Particle Size on Drug Solubility and Bioavailability
To bring it all together, a well-controlled particle size is critical to consistent bioavailability of certain products. Learn this information to understand the advantages and limitations of your mill.
You can read more from Rob by following him on LinkedIn.